半導体材料加工の基礎:ウェーハ・特殊形状加工フロー
半導体材料の加工
半導体とその関連材料は、まずは「インゴット」といった大きな塊として製造されます。
ウェーハや角形部品などの最終製品となるには、切断や研磨といった加工が必要です。加工工程はいわば「材料から製品へ」の第一歩です。
加工対象となる半導体および半導体関連材料には様々な種類が存在します。
- シリコン(Si):半導体デバイスの製造や、関連部材に
- 合成石英(SiO2):露光装置のレンズなどの光学部品として
- 炭化ケイ素(SiC):パワー半導体デバイスや製造装置関連部材に
- サファイア(Al2O3):半導体用の基板や製造装置窓材として
半導体材料とその関連材料には様々な種類がありますが、主な加工プロセスは共通しています。
半導体材料加工の基本工程
半導体・半導体関連材料の加工は大まかに、下記の3工程からなります。
- 切断加工:材料塊(インゴット等)を所望の厚さに切断する工程
- 研磨加工:砥石や研磨剤を用いて材料表面を磨き、平坦化する工程
- 成形・検査工程:研磨後の材料をさらに成形・加工する工程。また、所望の形状検査を行う。
基本的な工程はどの材料でも似ています。一方、加工する材料の特性や形状に合わせて、適切な切断・研磨方法を設定する必要があります。
切断工程
切断工程は「インゴット等の材料塊から、所望の厚さの材料を切り出す工程」です。
材料を切り出すだけのシンプルな工程に見えますが、高品質・高効率な切断には、切断ダメージ、寸法精度、材料の損失(カーフロス)などの要素を総合的に考慮する必要があります。
特に半導体材料のような硬くて脆い素材では、切断工程が後工程の品質や歩留まりに大きく影響します。そのため、用途や材料特性に応じて、内周刃ソー、ワイヤーソー、ブレードソー(ダイサー)など、さまざまな切断手法が使い分けることが重要です。
半導体材料の切断には、大きく2つの切断法が用いられています。
- ワイヤーソー(Wire saw)
- バンドソー(Band saw)
金属ワイヤーを往復させることで材料を切断する方式。ワイヤーと砥粒によって研磨的に削り切ることで切断する。ワイヤーにダイヤモンドなどの砥粒を付着させる固定砥粒方式と、砥粒を含む液体(スラリー)を流しながら切断する遊離砥粒方式がある。さらに、ワイヤーが1本のシングルワイヤーソーと、複数のマルチワイヤーソーに分類される。
金属製の帯状ブレードをループ状に回転させることで材料を切断する方式。ブレードには鋸歯がついており、機械的に切断する。
大まかに、バンドソーは「切断スピードが速いが、カーフロスが大きく低精度」、ワイヤーソーは「切断スピードは遅いが、カーフロスが小さく高精度」という特徴があります。
切断したい材料、求める性能によって適切な切断方法を利用することが重要です。
研磨工程
研磨工程は「材料から切り出した半導体材料の荒い切断表面を、研磨によって平坦化する工程」です。
切断された半導体材料の表面は、目には見えない微細な凹凸やダメージを含んでいます。これを精密に平坦化・鏡面化するために、「ラッピング」と「ポリッシング」という研磨が行われます。ラッピングとポリッシングの違いは以下の通りです。
種類 | 主な特徴 | 目的 |
---|---|---|
ラッピング (Lapping) | 中間仕上げ、平坦化 | 面の均し、ある程度の平滑化 |
ポリッシング (Polishing) | 鏡面仕上げ | 表面粗さの低減、鏡面化 |
ラッピングでは、加工対象物が所定の厚さになるよう、砥石や研磨剤を用いながら粗研磨します。ポリッシングでは、ウェーハ表面の凹凸を無くし、表面を鏡面研磨します。
研磨工程では、以下のような多様なパラメーターを制御する必要があります。
- 砥粒の種類
- 砥粒のサイズ
- スラリー濃度
- 圧力(加圧力)
- 回転速度
- 加工時間
加工したい材料の特性と必要な加工精度に応じて、適切な加工条件を設定することが重要です。
例えば、SiC(炭化ケイ素)やAl2O3(サファイア)は高硬度であり、難加工性です。ダイヤモンドといった適切な砥粒を選択して研磨を行う必要があります。
成形・検査工程
研磨された材料は、必要に応じてさらに加工されます。最終的には、所定の寸法や表面粗さを満たしているか検査が行われます。
半導体デバイス向けの材料は、通常は円形のウェーハ状に仕上げられます。一方で、半導体材料やその関連材料では、リング形状・四角形・微細な穴加工など、特殊な形状が求められることもあります。
このような特殊形状が必要な場合には、研磨工程の前後に再加工を行うことがあります。
再加工には通常、マシニング加工(機械加工)が使われます。半導体(関連)材料は脆く、割れやすいものが多いため、ワレやチッピングを避けるために、材料特性に適した加工条件の選定が重要です。
次の講座
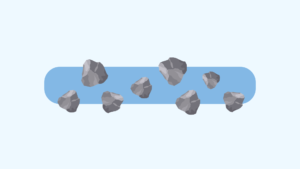